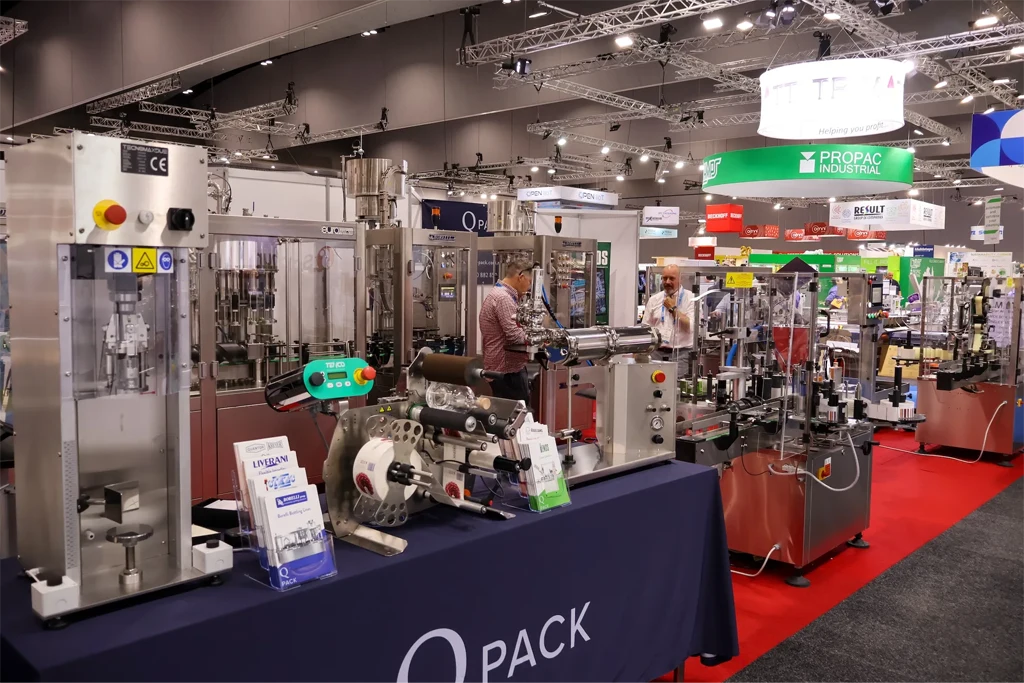
About the client
CCF offer a number of filling and packaging solutions to the beverage industry, providing contract filling services for a range of beverage types. Their range of commercial packaging equipment is able to produce still wine, cider, spirits, beer, carbonated beverages and more. CCF are capable of filling bottles and cans as well as blend, mix, batch and carbonate beverages.
Project background
In transitioning to a new facility, CCF aimed to revolutionise their operation. Central to their vision was the expansion of their business and elevation of their production capabilities. With this in mind, the team at CCF explored solutions that would both accomodate their growth plans but also enhance their service offerings. Recognising the important of catering to the diverse needs of their customers, they needed a solution that would integrate both bottling and canning capabilities into their operation while also having adaptable labelling solutions to accomodate a range of bottle and can specifications.
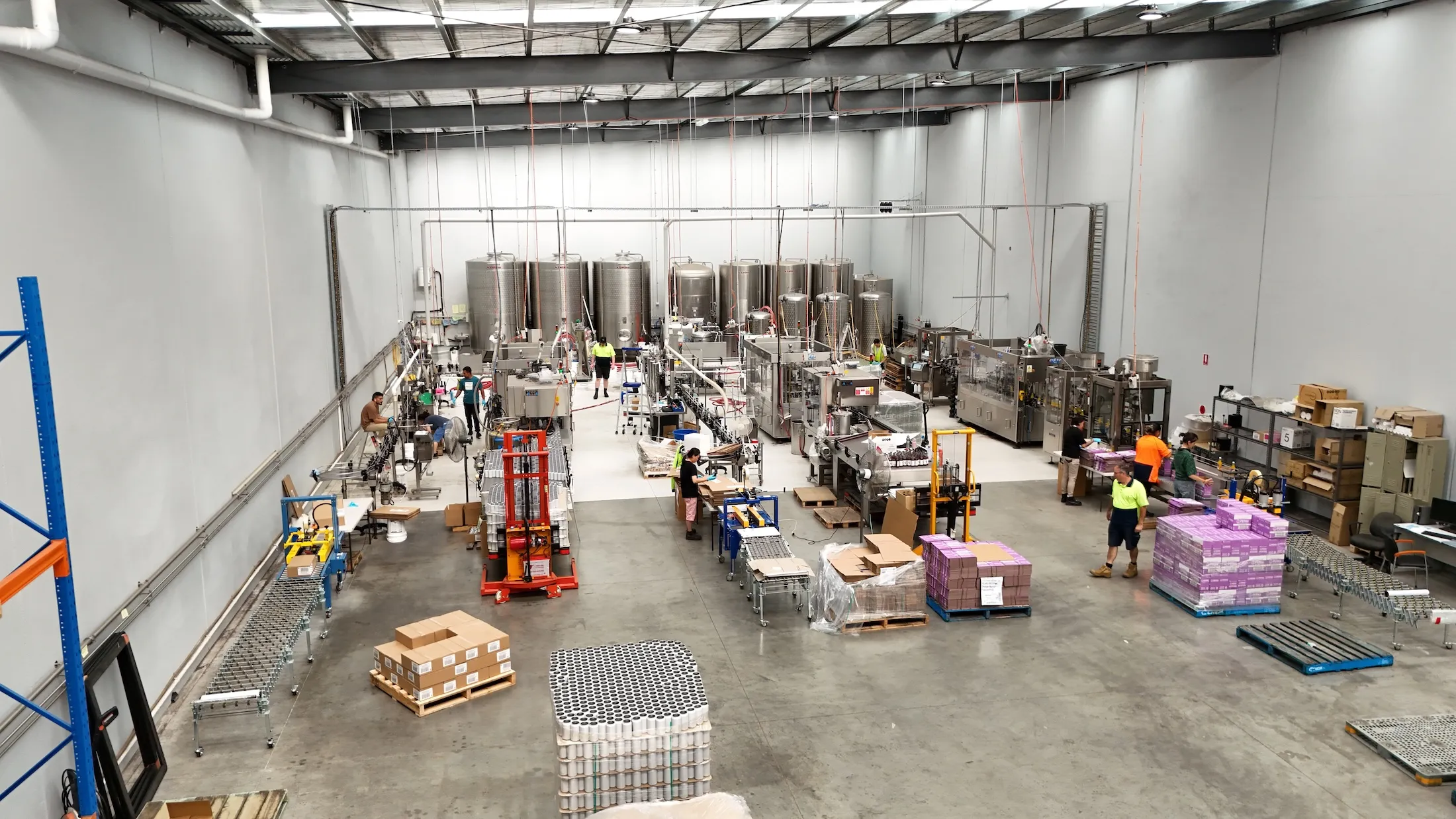
Innovative approach
Understanding the project brief, the team at Winequip/QPack recommended the implementation of three cutting-edge packaging lines designed to optimise efficiency and enhance productivity – which the team at CCF selected as its best option. Comprising of two CIMEC canning lines and one CIMEC bottling line, these state-of-the-art systems were completed with automated feed and accumulation tables, ensuring a seamless workflow and increase in production levels. Two of the three lines also feature ENOS labellers equipped with coders to complete the packaging process. In recognition of the requirements of the bottling line, a Borelli FUTURA screw capper was also installed.
To complete the setup, Gortani & Letina tanks ranging from 2000 to 10,000 litres in capacity were also included. These tanks are used to blend, mix, batch and carbonate customers beverages exactly to their requirements. Additionally, Kreyer refrigeration units were incorporated into the tank setup to ensure precise temperature control throughout the production process.
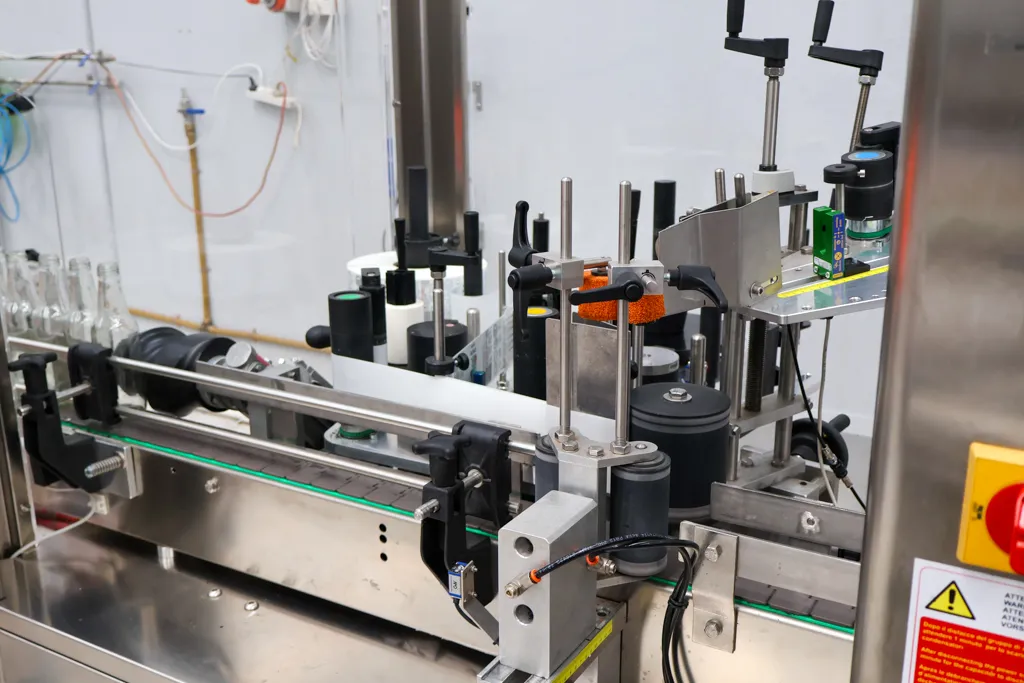
Key units installed
CIMEC Isobaric Canning Line
- Fully automatic rotary isobaric canning lines that include rinser, filler and seamer with automatic lid dispensing system.
- Designed for beer, cider and other carbonated beverages that are sensitive to oxygen degradation.
- It has a multiple CO2 injection valve that reduces oxygen in the can to negligible levels.
CIMEC Isobaric Bottling Line
- Available as a freestanding filler or a complete monoblock with rinser, filler and capper.
- Suitable for both glass and PET bottle formats.
- Offered with an electro-pneumatic process, allowing for complete control during filling phases.
Enos Speedy Labeller
- Linear labeller with up to 4 stations and max output of 3000bph.
- Equipped with step motors and electronic variable speed drive.
- Suitable for front and back labels on round bottles in a variety of different formats.
Enos C5000 Labeller
- Automatic linear labeller rated up to 5000bph with one label.
- Options include front and back label on separate stations and mignon formats.
Borelli Futura Screw Capper
- Speeds of up to 2800bph.
- Alternate models include cork, ROPP, crown caps, pick & place, PET caps or GPI formats.
- Available in monoblock or freestanding form.
Gortani & Letina Tanks
- The most versatile solution for carbonated beverages.
- Letina tanks rated at 2 bar and Gortani at up to 12 bar.
- Both manufactured in 304 stainless steel.
Kreyer Refrigeration
- Developed specifically for the beverage industry.
- Ideal for cooling or temperature control of beverages during manufacturing process.
- Reversible units can also warm-up beverages before bottling.
- Additional Fermflex units highlight actual and required temperature as well as mode of operation.
Results
Collectively, this packaging line installation at CCF was able to position them for a significant increase in productivity and capabilities. Through utilising the latest innovations from our key industry suppliers, CCF is now best placed to meet evolving consumer demands while upholding their commitment to quality and excellence.
Thanks to the team at CCF for participating in this case study. Contact CCF to learn more about their contract bottling/canning options using the below details:
- https://www.ccf.net.au/
- sales@ccf.net.au
- (03) 9305 4258
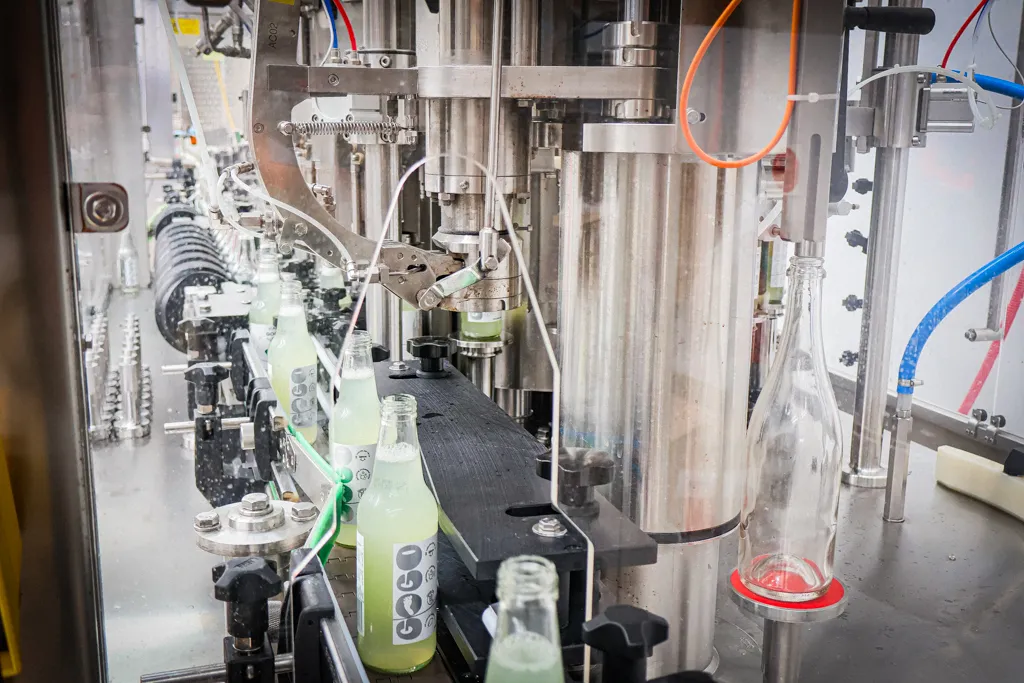